Unlocking Efficiency: Improving Labor and Supply Chain Operations for a Sporting Goods Retailer
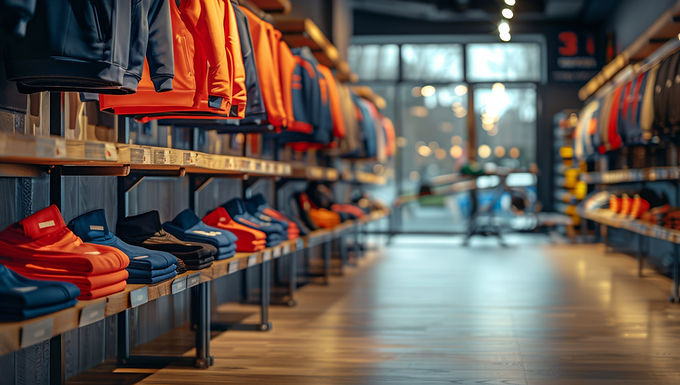
A sporting goods retailer with over 1,000 stores was struggling with inefficiencies in its supply chain and labor management. The company faced challenges in improving operational metrics such as cartons per labor hour (CLPH) and labor allocation. Inefficient freight management processes consumed excessive labor hours, reducing the company’s ability to maximize productivity and profitability. These issues were impacting the retailer’s ability to scale and operate efficiently.
A comprehensive analysis of the supply chain and labor management processes was conducted, leading to the development of integrated IT, reporting, and staffing solutions. By optimizing freight management processes and labor allocation, the retailer was able to reduce inefficiencies and unlock additional capacity. A new approach to tracking cartons per labor hour (CLPH) was implemented, along with reallocation of labor resources to focus on higher-value tasks.
The sporting goods retailer achieved a 30% improvement in CLPH, unlocking 23% of the labor previously tied up in freight management. This allowed the company to reallocate workforce efforts to more strategic initiatives, improving overall productivity. The streamlined processes and improved labor allocation enhanced operational efficiency, allowing the retailer to better manage inventory, reduce costs, and improve store performance.