Bridging Data Gaps: Achieving Operational Efficiency through End-to-End Visibility
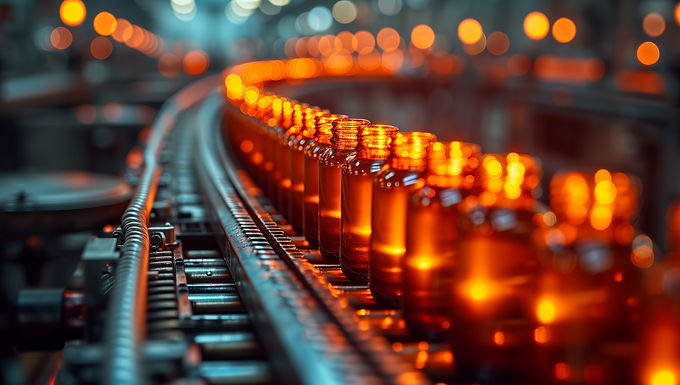
A leading food manufacturer across the Americas faced operational inefficiencies and data visibility challenges. Senior leadership struggled to gain a clear picture of the company’s performance across various functions, from sourcing to manufacturing. Data was scattered across systems, and the company lacked a unified view of production and operational processes, leading to delays, production constraints, and customer dissatisfaction. These issues hindered the company’s ability to meet demand and improve its operational efficiency.
To address these challenges, the project focused on bridging the gap between strategy, data, IT, and operations. By leveraging a detailed value stream analysis, the team was able to map out the end-to-end processes and identify bottlenecks. Over 50 operational stories were identified and prioritized, and wireframes and specifications were developed for system improvements. These enhancements included reengineering processes to eliminate constraints and provide full dashboard visibility to stakeholders across commercialization, manufacturing, warehousing, and finance.
The company achieved significant operational improvements, including the elimination of production constraints across multiple areas, reduced cycle times, and improved overall efficiency. End-to-end visibility across departments empowered leadership to make data-driven decisions, enhancing collaboration and alignment. The reengineered value stream processes improved production timelines, reduced delays, and restored customer satisfaction. This transformation allowed the manufacturer to operate more efficiently and respond better to market demands.